
PHD


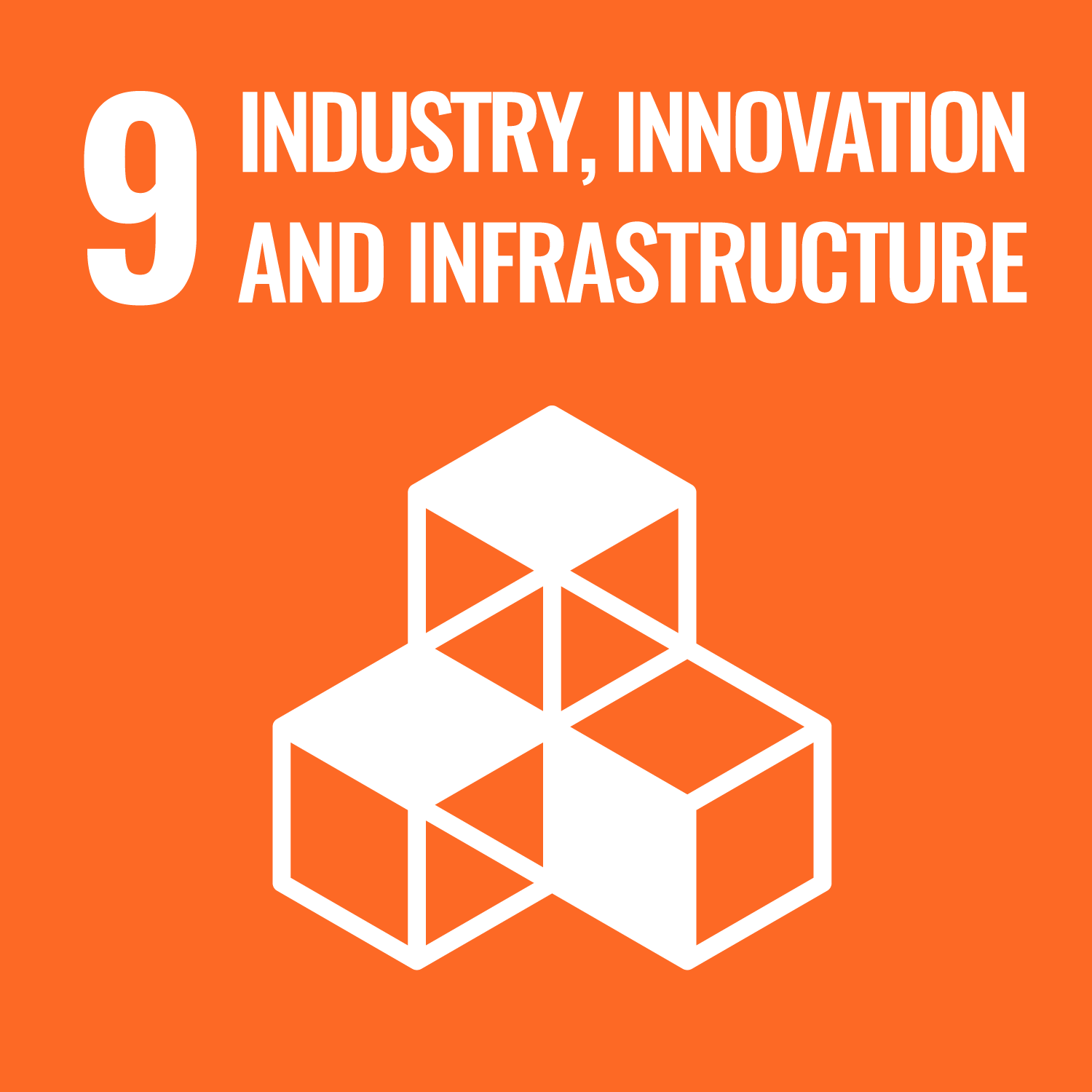
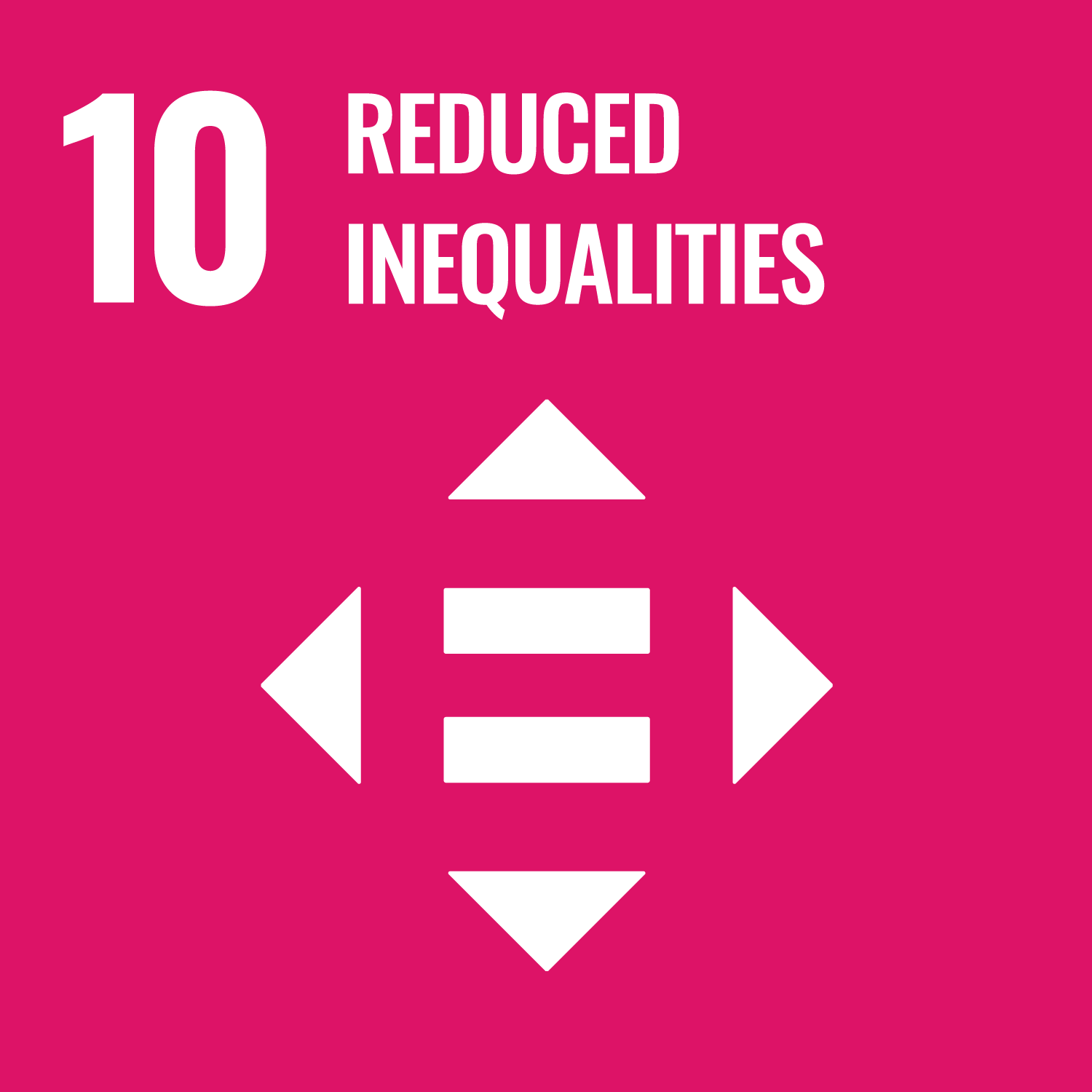
AiM2Xl - Project 3B
Additively manufactured parts have highly anisotropic microstructure resulting in bad/directional mechanical properties. This problem roots in the input heat. During laser additive manufacturing, directional printing of the layers of molten material results in directional creation/growth of microstructure after the solidification. Apart from anisotropic properties, defects (such as porosity) are other disadvantages of additive manufacturing.
Improving the final microstructure by adjusting the input parameters, including device parameters (e.g. laser) can solve or ameliorate these disadvantages of (metal) additive manufacturing. To do this, a numerical thermo-metallurgical model is indeed necessary to address changes in the microstructure as a result of changes in device setup. Using this tool, it could be possible to find the optimal input parameters (Laser settings) to reach the desired microstructure/mechanical properties.